シリコーンゴムの2次加硫とシロキサン対策の全点実施と経験実績
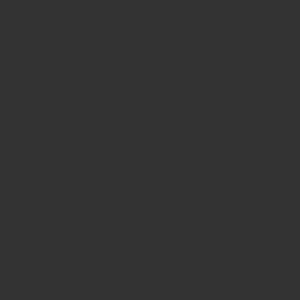
当社の製造するシリコーンゴム製品は全て2次加硫を施して残留シロキサン対策を行っております。時に精密電子製品に障害をもたらす低分子量シロキサンを徹底除去して安全安心なシリコーンゴムを供給しております。
シリコーンゴムの2次加硫とは?
シリコーンゴム成形を金型内で成形することを「1次加硫」と称します。成形品は製品形状になり一見完成品のように見えますが まだ製品内部には加硫剤などの残留物などが残存しております。
「1次加硫」済みのシリコーンゴム製品を、強制排気装置が付いた恒温槽BOXに投入して、200℃~220℃の高温下で2時間~4時間の熱処理することを「2次加硫」と言います。投入時間は製品のボリュームや使用環境を想定して延長することがございます。
![]() |
![]() |
![]() |
![]() |
シリコーンゴムの2次加硫の必要性
テレビのリモコンのボタン部分などにシリコーンゴムがコンタクトラバー(接点ゴム)として使用されています。ボタンを押すと内部の基板にスイッチが入って動作する仕組みにです。
このコンタクトラバー(接点ゴム)に2次加硫が施されていないと 時間経過と共にシリコーンゴムから残存している低分子量シロキサンが揮発して基板の上にうっすらと堆積してしまいます。
堆積した低分子量シロキサンが絶縁のため導通障害を発生させてしまいます。電気製品全般に注意しなくてはならない現象で 故障の要因の一つとして検証が必要になる場合がございます。
シリコーンゴム製造では「1次加硫」「2次加硫」は常識のセット工程となっております。当社はもちろん「2次加硫」を行わないことはありません。 電子製品に限らず、どのような活用シーンでも安心安全にご使用いただけます。
![]() |
![]() |
低分子量シロキサンとは?
シロキサンとは(-Si-O-Si-)nを分子骨格に持つシリコンの原料のことをいいます。この環状シロキサンの結合が長く大きくなったものを高分子シリコーンといいます。
低分子量シロキサンは、シリコーンオイルや成形後シリコーンゴムなどのシリコーンゴム製品となった後にも微量に製品に残ってしまったものです。(不純物ではありません)
この低分子量シロキサンの結合量によりD3(三量体)、D4(四量体)、D5(五量体)などと表記されます。この量体が何個あるかで何量体かが決まります。D20までを低分子量シロキサンと称します。特にD3~D10までの量体が電気接点障害を引き起こす原因となります。
量体の数字が大きくなると沸点が高く、逆に量体の数字が小さいと沸点が低くなります。
主な量体
D3 C6H18O3Si3 融点64℃ 沸点134℃の固体
D4 C8H24O4Si4 融点18℃ 沸点175℃の半固体
D5 C10H30O5Si5 融点-30℃ 沸点210℃の液体
低分子量シロキサンは高沸点物質だが揮発性が高いため、室温あるいは各地の自然環境でも蒸気となって空気中へ拡散します。拡散した場合に問題が起きてしまいます。
この残留した低分子量シロキサンを強制的に沸点の環境に投じ、低分子量シロキサンをこれ以上揮発しないまでに出し切ることで安定したシリコーンゴム製品になります。
この強制的な熱処理が「2次加硫」でありシリコーンゴム製造には欠かせない工程となってます。
2次加硫の効果
シリコーンゴム成形品を2次加硫することにより、低分子量シロキサンの残留量が減少しますが、それは、2次加硫の温度・時間・成形品の厚みで比例していきます。
顧客の品質基準として、低分子量シロキサンの残留量も規格として明確にする場合もございます。その多くは、D4~D10の量体の低分子量シロキサンの残留量の合計が1,000PPM以下となっているところがほとんどで機能上問題ない管理値となっています。
一つ例をあげますとゴム部品がデバイス内の密閉空間内にあると、シロキサンによる基板等への腐食には不利となり、密閉空間外であれば同現象が生じる可能性は低くなります。これらは、電子部品メーカー様、家電・オーディオメーカー様からの要求値で、半導体の製造装置、検査装置のお客様等はさらに厳しい基準(D4~D10・300PPM以下)を設けていらっしゃる所もございます。
2次加硫の品質維持管理体制
このようにシリコーンゴムの成形加工において、「2次加硫」工程は重要です。”工程を行うもの” と “工程を行わないもの” が混在しますと間違えの元になりますので当社では全点実施しております。
「2次加硫」を全点実施しておりますが 低分子量シロキサンの残留量を毎回測定しているわけではありません。
この低分子量シロキサンの残留量を測定するには、ガスクロマトフィー等の 分析手法を用いなければ測定できないため、破壊検査が必要です。測定に多大な時間と費用を要してしまうため、頻繁に測定することは事実上不可能です。
よって、当社では2次加硫工程を『特殊工程』と位置づけ、管理すべき内容を明確化させ、工程の妥当性確認を行っております。
ご要望により有償で残留シロキサン量の測定をすることは可能です。(外部検査機関にて)
![]() |
![]() |
![]() |
当社の2次加硫工程の管理項目
資格 2次加硫工程の作業者は、定められた教育・訓練を受けた資格認定職とし、必要な技能・力量を有する者のみが携わることを可能としています。当社の品質マネジメントシステム内の「教育・訓練規定」に基づき、2次加硫工程は資格認定職とし、最終的には、製造技術課長が承認した力量のある者が携わるシステムとなっています。 |
![]() |
強制排気 2次加硫工程時、BOX炉内は強制排気を必須とし、気化された低分子量シロキサンがシリコーンゴムに再付着しないようにしています。強制排気を行うとBOX炉に設定した温度まで上昇するのに時間がかかることは事実なのですが、強制排気を行わないと、せっかく熱処理で揮発したシロキサンが、炉外に放出されず、ゴム製品に再度付着し、結果的に残留シロキサン濃度が高いままといった現象になってしまいます。 ※恒温槽全機の排気用ダクトの分解清掃、及び排気用大型シロッコファンの分解清掃&メンテナンスを外部専門会社に委託し実施済み。2024年8月24日実施 |
![]() |
投入量管理 BOX炉内に一度に投入可能な製品の最大量を制限する事でシリコーンゴムからのアウトガスが炉内からの排気が不十分にならないよう、容量管理を実施しています。過去の2次加硫条件と残留シロキサン量の測定データを分析した結果、BOX炉内に製品を入れすぎてしまうと、いくら機械的に強制排気を行っても、揮発したシロキサンが炉外放出しきれず再付着となって、濃度が高いままとなってしまいます。分析の結果、最大でも炉内の容積に対して、60%までとして、管理を行っています。 |
![]() |
チェックシート 低分子シロキサンが結晶化し、BOX炉内に残留してしまうことによる異常を防止するため、毎日作業前に行う清掃と週に1回行う大清掃の項目の明確化とチェックシートを用いた実施確認を行っています。当社の品質マネジメントシステム内の「設備管理規定」に基づき、BOX炉の清掃結果を品質記録である点検表に記載し、清掃漏れを防止するとともに、清掃が確実に実行されたか、部門長がチェックします。 |
![]() |
設備点検 BOX炉の定期点検を行い、温度上昇異常、温度分布異常の発生を防止することで、機械的影響による、品質異常を未然に防ぎます。年1回、温度計を用いてBOX炉内のコーナー、中心部の計9箇所の温度測定し、機械的な異常がないか確認しています。 |
![]() |
お問い合わせ
シリコーンゴムは有機合成ゴムに比べ、特に耐熱性、耐寒性にすぐれ、更に耐候性、熱伝導性、電気特性、反発性等がはるかに優れています。特に耐候性に関しては、耐候性試験を10年以上続けても劣化がほとんどなく、試験結果より推定すると100年程度でもゴ[…]
私たちの会社では、シリコーンゴム製品の可能性を追求しています。 シリコーンゴム優れた特徴として 高度な耐久性・耐熱性・対オゾン性を持ち合わせます。更に電気特性・非粘着性にも優れ、精密電子機器部品、自動車関連部品・医療関連機器・食品関連[…]
「品質は良くて当たり前」顧客からはそう言われていますし、当社もそう認識しており品質維持は最優先に取り組んでおります。 当社はシリコーンゴムの持つ特性をよく理解しているからこそ、モノ造りの課程で生じる障害や難題を最短で解決することができ[…]